金型が動作する様子をイラストでご説明します
※ オランダの絵本のような配色になってしまいましたが、意図的ではありませんのでご容赦ください
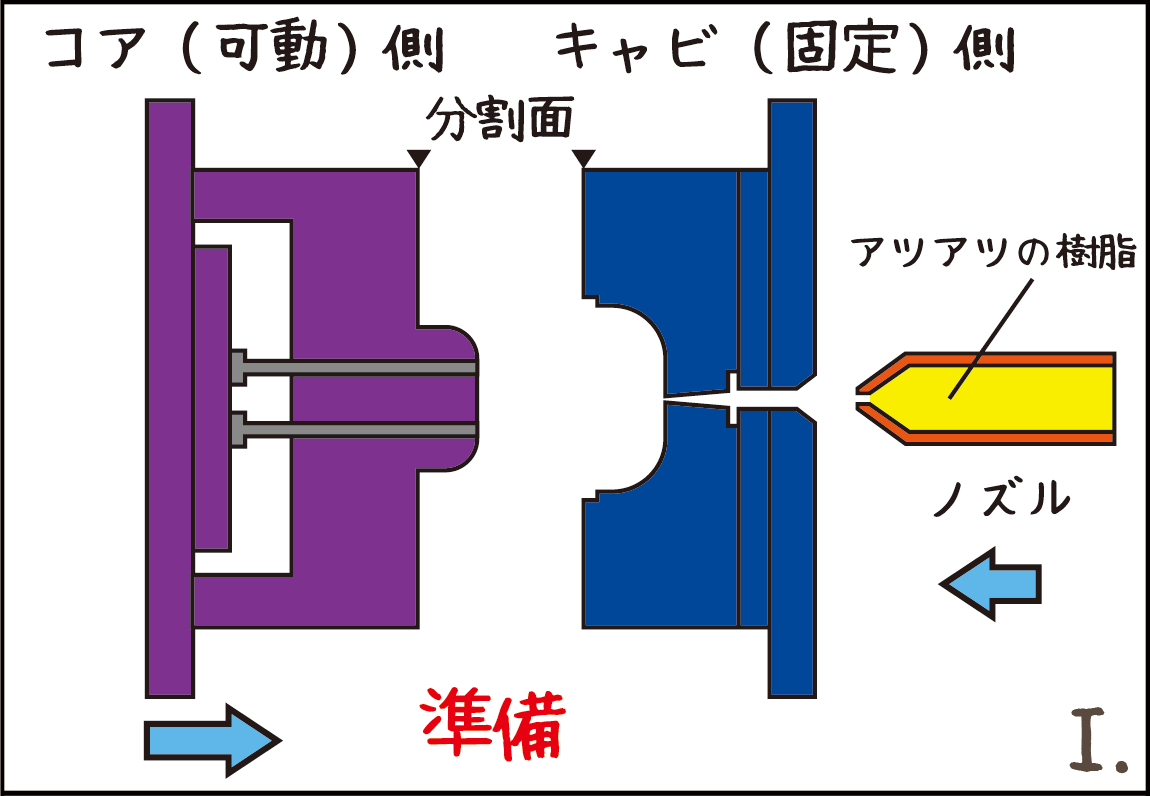
ノズルと密着して樹脂が注入される部分が動かないことから、青色の構成要素を固定側もしくはキャビ側(キャビティー)の金型と表現されます。固定側に押しあてる動きをする紫色の構成部は、可動側もしくはコア側の金型と呼ばれています。
成形の1回目から完璧な形状のものが射出されることは、まずもって有り得ないでしょう。実際には何度も成形条件(後述します)を変えながらテストを行い、もっとも理想に近い形状で量産できるようトライ&エラーを繰り返しますが、ここで時間を費やすと発売予定にも影響が生じます。
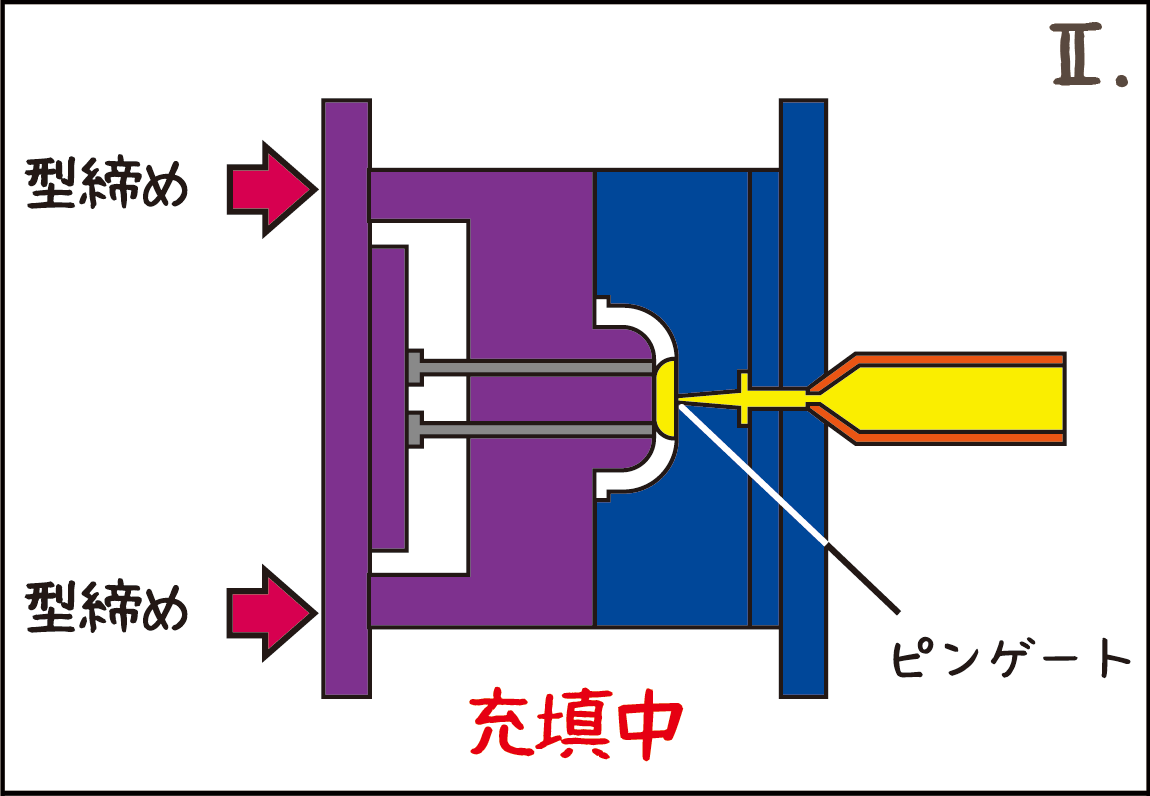
(イラストでは省略されていますが)金型の四隅にガイドが立っているので、基本的に金型が分割面(鉛直)の方向でズレることはありません。しかし、ゲートと呼ばれる小さな射出口を介して製品部分に樹脂を流し込み始めると、前述のような要因で水平方向に金型が開こうとするため、猛烈な圧力を加えて金型を締めてやる必要があります。
分割面に微細な隙間が生じるとバリと呼ばれる余剰な部分が生成されてしまうので、製品形状や樹脂量に照らして充分な型締め力を有した成形機を選択している必要があります。
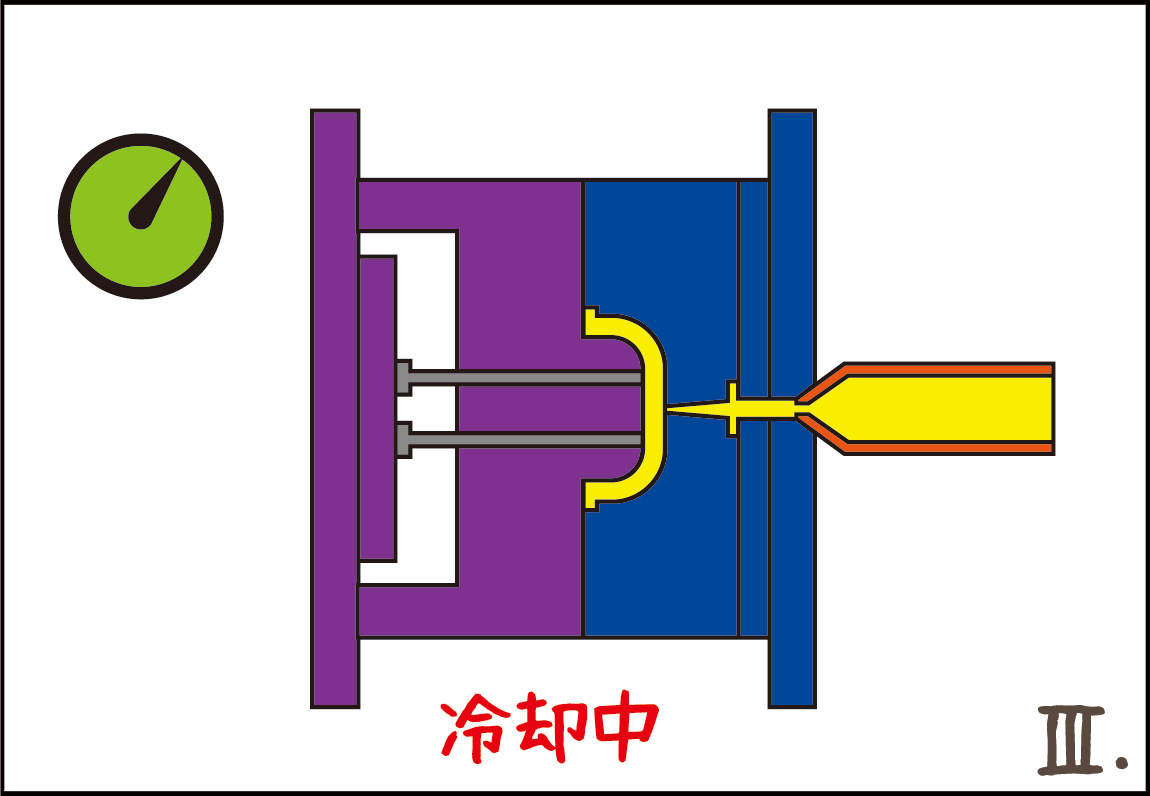
樹脂の種類や製品形状に適した時間をかけて金型内部を冷却します。成形条件は冷却時間の長さだけでなく、樹脂の温度や注入する量と速度、押し出す圧力などの様ざまな要素が組み合わさるので、最終的な成果物を計測して問題の原因を予測しながら、最適となる成形条件の組み合わせを探ります。
内部に残留応力が残っていたり、冷却時間が十分でなかったりすると、成形後に変形を生じてしまう可能性が高まります。冷却の完了までには多くの数値制御が必要であり、成形機をオペレーションする担当者の経験や技量に委ねられます。
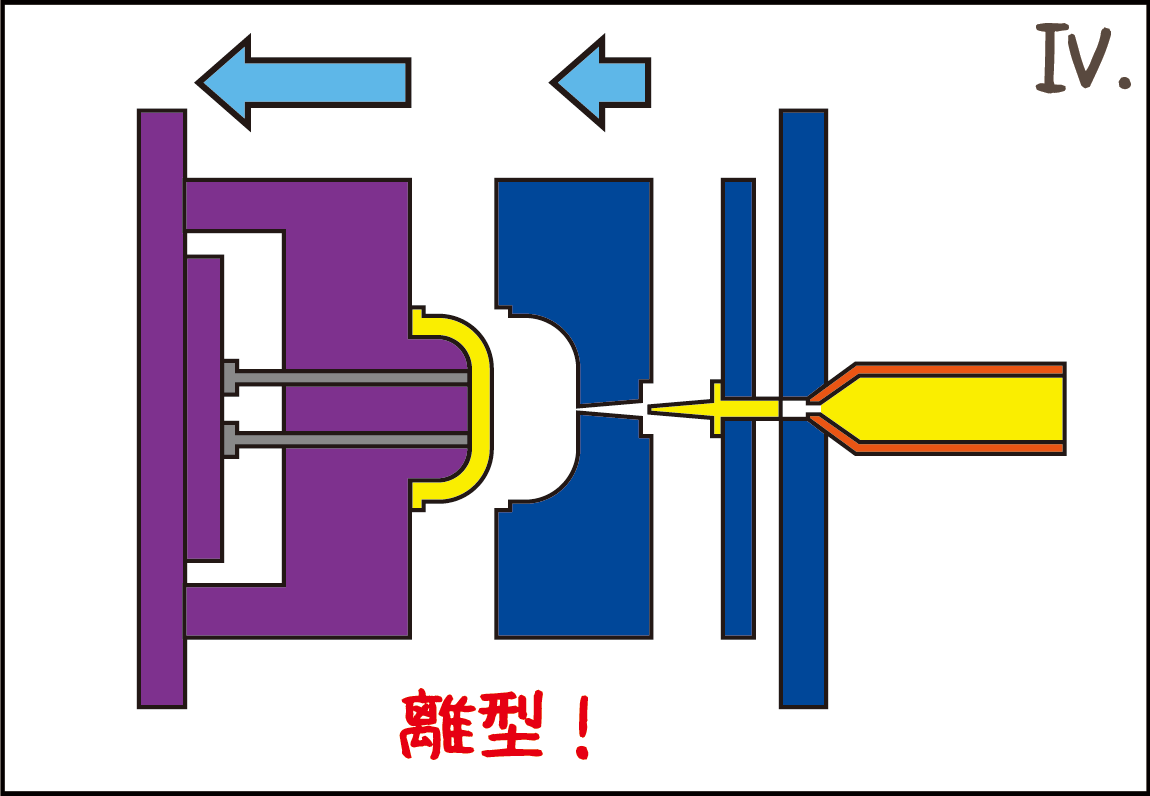
冷却が完了すると、コア側の金型が開放する方向に移動して、コア側に貼りついている製品がキャビ側から離れます。
イラストのようにピンゲートで充填される場合は、離型が開始されると自動的に不要な部分(スプルー)が製品から切断されます。(多数個取りで用いられる)サイドゲート方式では、樹脂を届ける水路の役割をはたすランナーが製品と繋がったままの状態なので、後工程で切断する作業が必要になります。コア側から注入するサブマリンゲートと呼ばれる注入方法では突出し時にゲートが切り離されます。
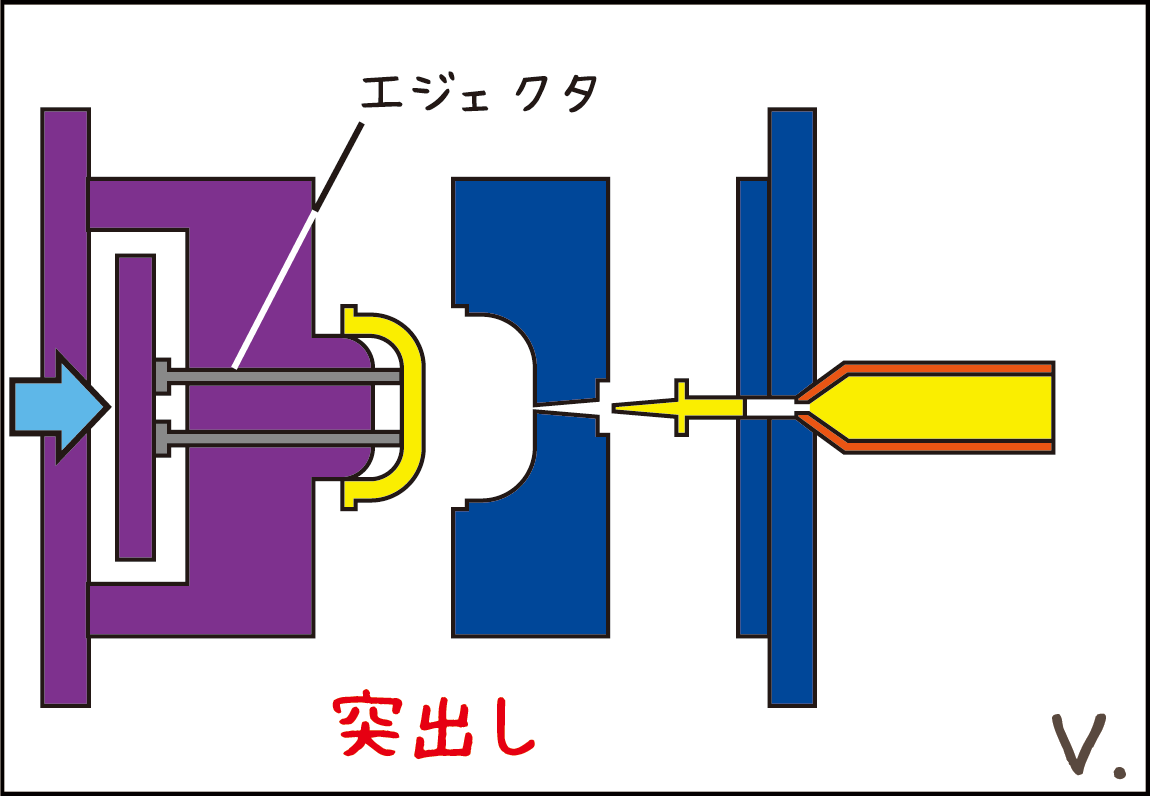
コア側にひっ付いている製品を取り外す目的で、エジェクターと呼ばれるピンが強制的に浮かせて引き離す工程があります。コア側が完全に開く直前に、バネによってエジェクターピンが金型の分割面から何本も飛び出してくる様子が見られるはずです。エジェクターの端面の輪郭が転写されてしまうので、意匠面で目立たせたくない場合は、事前にピンの形状や位置を相談しておかなければなりません。
キャビ側では2番目の金型(プレート)が発するカッコンカッコンという音とともに、不要部分となったスプルーが取り外せる状態になっているはずです。
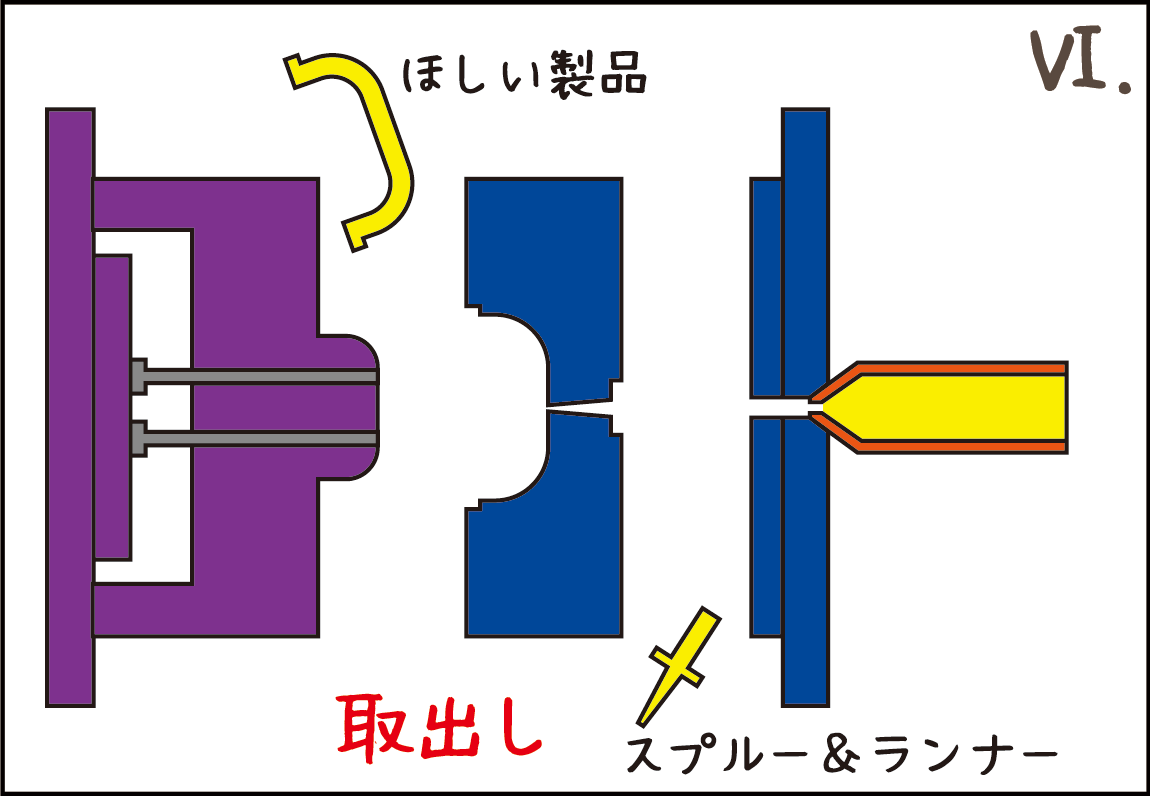
製品やランナーなどの生成物は、成形機に専属の作業員が手で取り出すこともありますが、省力化の目的でトラバースと呼ばれる取り出しの設備を使うこともあります。または、そのまま自由落下させて一定量をケースに貯めておく場合もあります。
成形の直後は製品内部に熱が残っているため、完全に内部まで一定温度となった段階で寸法や製品形状を評価します。成形条件では不具合に対処できない場合には、金型を修正することになります。
評価結果に問題が無ければⅡ~Ⅵの工程を繰り返して、量産性に耐えうるか最終判断します。